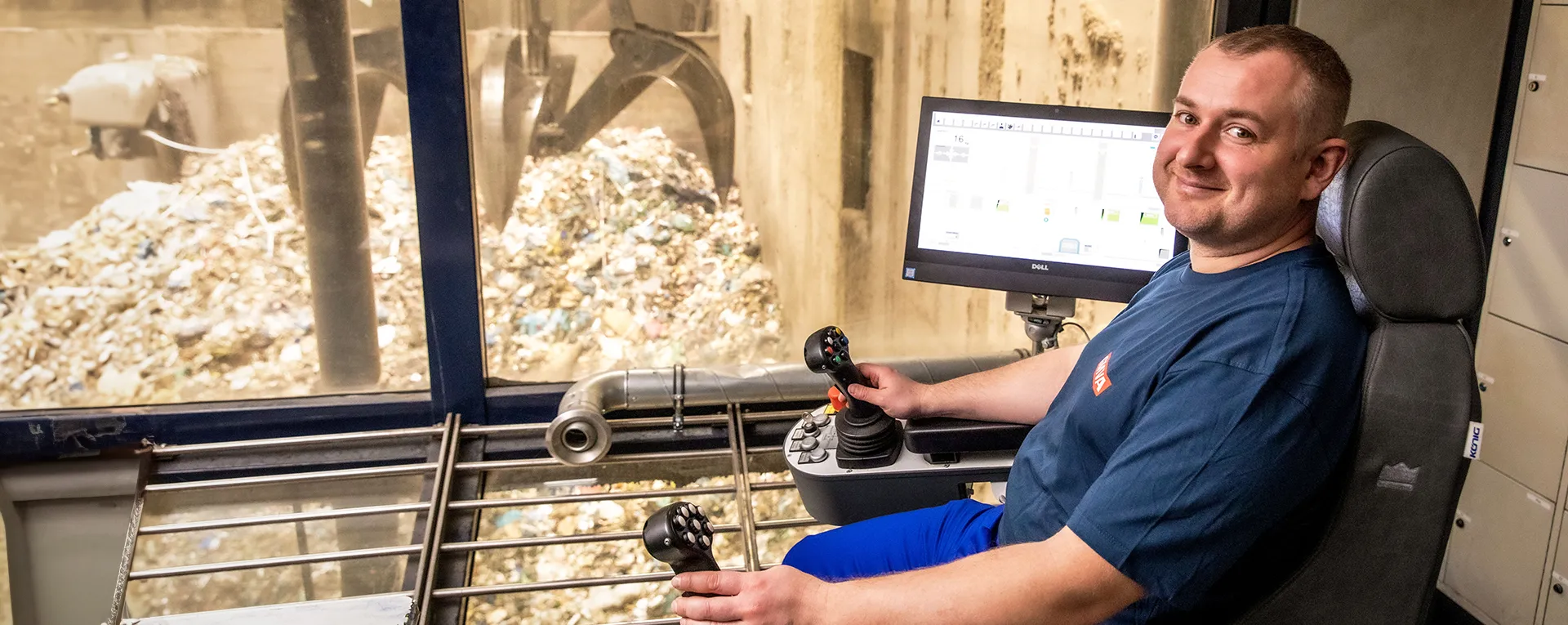
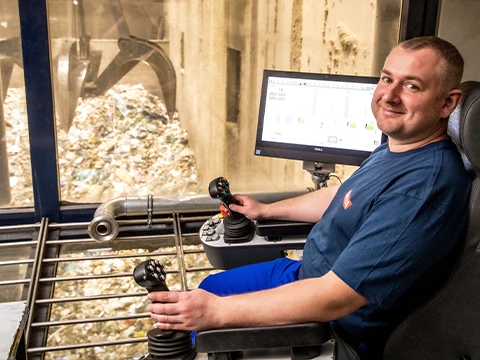
We make the best out of waste: energy that is environmentally friendly!
For over 50 years, the Gemeinschafts-Müll-Verbrennungsanlage Niederrhein (GMVA) has ensured the environmentally friendly treatment of waste and commercial waste subject to mandatory disposal. As it converts most of this waste into energy, it is also an important producer of electricity and district heating. Established in 1972 through the conversion of the Concordia Bergbau AG coal mine power plant, GMVA is a company with a real Oberhausen tradition. Accordingly, we have close ties to the people and the region.
Operation
GMVA operates as a public private partnership (PPP) between the cities of Oberhausen and Duisburg and the environmental service company, REMONDIS.
A total of 200 dedicated and, in some cases, highly specialized employees work at our company to ensure that operations run smoothly, safely and sustainably.
Up to 700,000 tons of waste are thermally treated here every year. State-of-the-art flue gas cleaning systems ensure that mainly water vapor is released into the environment via the chimney. This is well below the legal limits.
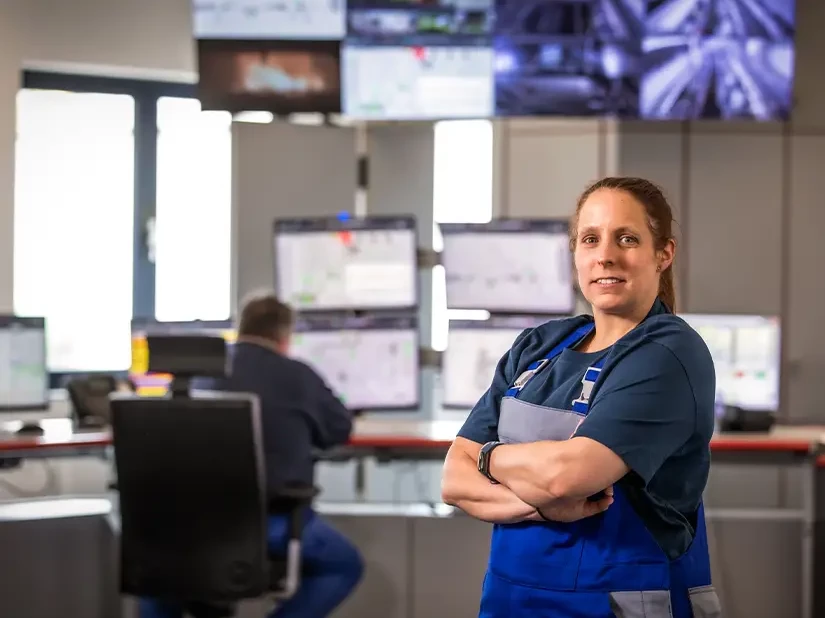
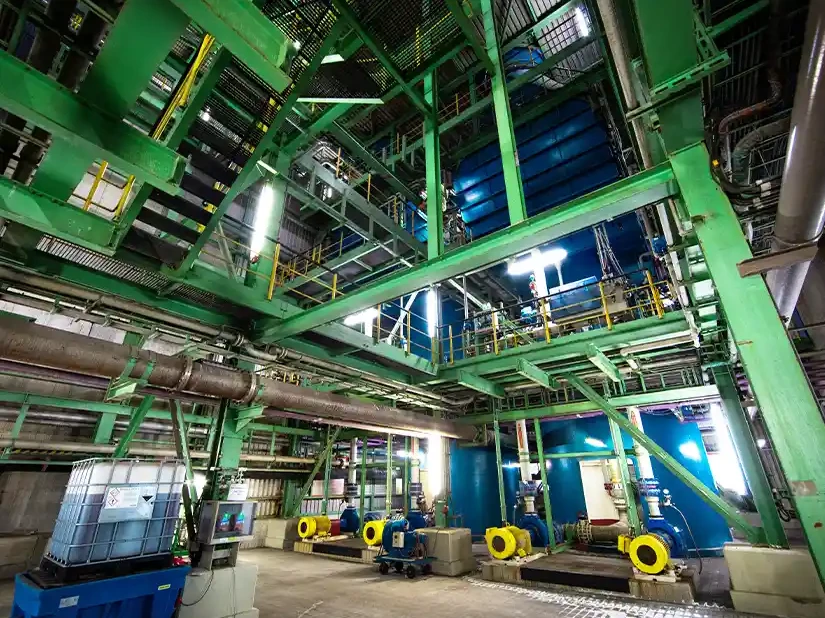
With all our energy forthe environment and the region
Despite the highest recycling standards, enormous quantities of waste are produced in Germany that cannot be reprocessed – i.e. cannot be recycled. This is precisely why controlled, strictly monitored incineration is a sensible solution. As it produces environmentally friendly electricity from unavoidable waste heat, it also makes a contribution to the energy transition. GMVA supplies around 100,000 households in Oberhausen with electricity from the energy generated by the thermal utilization of waste. Thanks to the combined heat and power process during incineration, it also supplies a significant proportion of the district heating for the city of Oberhausen’s district heating network.
Discover the facility on your own
If you’ve always wondered what’s actually behind every single building on the GMVA site, we invite you to take a trip through our 3D model:
And this is how it works:
– Simply hold down the right mouse button and the facility can be rotated in all directions
– Use the + and – buttons at the bottom left to zoom in or out
– Click on one of our buildings to find out everything about it
– You can select the most important parts of the facility directly from the menu
Waste bunker
The bunker has a storage capacity of 26,000 m3 and can be filled via ten tipping points with hydraulically operated sliding beds. There are two waste shears and three crane systems in the bunker area itself. The crane systems have two functions. Firstly, they are used to shift the waste so that the combustible mixture is as homogeneous as possible. Secondly, they are used to fill the four boilers. The grab of one crane system can hold around five tonnes of material. The cranes are operated around the clock in 5-shift operation. This ensures that the system is in operation 365 days a year.
Waste water treatment plant
The scrubbing water from the flue gas scrubbers is purified here. The heavy metals contained are pH-selectively precipitated from the desalting quantities from the first scrubber stage (> HCl scrubber). The wastewater from the second treatment stage is mixed with the wastewater from the first stage in a further process to produce a gypsum suspension.
Evaporation plant
The wastewater produced is concentrated to approx. 25 % of the original volume. The distillate resulting from the evaporation process is recovered and reused as process water in the plant. The remaining brine contains approx. 5 – 8 % solids (mainly sodium chloride).
Slag bunker
As soon as the waste is incinerated at over 1000 degrees, nothing remains except a little slag. This is transported via conveyor belts to the slag bunker. There it is loaded onto lorries by crane, which collect the slag for further processing. The slag is used in road construction, for example, and can therefore be reused.
HCl scrubber
In the first scrubbing stage of the flue gas scrubber – the so-called HCl scrubber – hydrogen chloride, residual dust, heavy metals and dioxins are removed from the flue gases in an acidic environment (pH< 1).
SO2 scrubber
The SO2 scrubber takes on other acidic pollutant components and separates them out of the flue gas. Here, sodium hydroxide solution is used to bind the sulphur dioxide with washing suspension to form sodium and calcium sulphite in the form of salt.
Fabric filter
Our system is equipped with modern fabric filters, which are made up of approx. 5.5 metre long filter bags. The filter material used is fabrics and felts made of fibres, which are processed into bags. The flue gases flow through these bags. A filter cake forms on the outer surface due to the addition of additives. This filter cake serves as the first barrier through which the flue gases must pass before they reach the fabric of the filter bags, which reliably retains particles. The additive used also has the special property of binding and effectively removing substances such as dioxins, furans and heavy metals from the flue gases through adsorption.
Firing
The waste is fed into the four combustion boilers via feed hoppers. They are the centrepiece of the plant and reach temperatures of up to 1,200 °C in the main combustion zone. Inside the boilers, the material is transported on a roller grate through five different combustion zones. Specifically, these are drying, degassing, ignition and the main combustion and burn-out zones. All four combustion lines together have a total firing capacity of 270 MW. The 17th Ordinance of the Federal Immission Control Act stipulates that the resulting reaction gas must be kept at a temperature of at least 850 °C for at least two seconds after the last combustion air supply to ensure that dioxins are safely destroyed.
Control centre
Nothing happens unobserved in the incineration plants. All processes are seamlessly monitored by our specialists – 24 hours a day, 365 days a year. All measured values from boiler operation and flue gas cleaning are collated in the central control room. The specialist staff working in shifts permanently monitor, record and analyse all process data and then archive it. If necessary, immediate intervention in the system control is carried out directly from the control room.
VE plant
The VE plant (Full desalination plant) is used for thermal waste treatment and removes all dissolved salts and minerals from the water used to generate steam. This is necessary to prevent deposits and corrosion in the boiler tubes, which increases the efficiency and service life of the system. Ion exchange produces high-purity water that is ideal for operating the steam turbines.
Turbine
Combustion converts the chemical energy released into thermal energy. The flue gases, heated to 1,000° C in this way, transfer their thermal energy to the water vapour system. The steam produced in the boilers is fed to the two extraction condensing turbines to drive the generators connected to them. If required, some of the steam is extracted upstream of the condensation section of the turbines to extract district heating – in the order of up to 150,000 MWh per year – in the combined heat and power system. The other part of the steam flow enters the final stages of the condensation section of the turbines. The vapour, which has been expanded into a vacuum, is then condensed in the condenser and fed back into the boilers.
Cooling towers
In order to close the power plant’s water vapour cycle, the steam that is not completely condensed in the turbines must be condensed in the condensers as water vapour. Two cooling towers with 9,000 and 4,000 m3 of water circulation per hour respectively ensure the recooling of the condensation heat released.
Chimney
Our 140 metre high chimney has almost become a landmark in Oberhausen and the surrounding area. State-of-the-art flue gas cleaning systems guarantee that virtually clean air is released into the environment via the chimney. The strictest controls and regulations ensure that emissions are always many times below the permitted limits in all respects. Proof of this are the peregrine falcons that breed there every year and have been using the top of the tower as a breeding and rearing centre since 2016.
Electrostatic precipitator
Each boiler has its own flue gas cleaning system with a capacity of 131,000 m3 per hour. After leaving the boiler, the flue gases are fed directly to the electrostatic precipitator, where the dust is separated from the collecting surfaces by means of an electrostatic field.
Scale
Each vehicle is weighed before and after delivery of the load. The difference corresponds to the amount of waste delivered, which is invoiced to the deliverer or producer.
Also a sought-after partner beyond the region as well.
Extensive capacities, a professional team of employees and state-of-the-art plant technology that meets the highest environmental standards make GMVA a sought-after contact point far beyond the city limits. In addition to the waste from Oberhausen and Duisburg that is subject to mandatory disposal, waste from the districts of Kleve, Steinfurt and Coesfeld is also recycled here. In addition, pre-treated commercial waste from regional and national sources is delivered by REMONDIS – one of the world’s largest recycling, service and water companies.
No way – Just hot air! Clean energy.
In addition to electricity, GMVA also produces district heating. This is fed into the grid and supplies numerous private households and commercial operations. Depending on requirements, between 15 and 25 million liters of heating oil can be saved each year.
Overview of services | |
---|---|
Delivery quantity | 680,000 to 720,000 t/a |
Vapour generator quantity | 2,200,000 t/a |
Total electricity generation | 390,000 to 420,000 MWh/a |
Electricity consumption | 75,000 MWh/a |
Electrical grid feed | 315,000 to 340,000 MWh/a |
District heating quantity | 50,000 to 150,000 MWh/a |
Average waste calorific value | 10,500 kJ/kg |
Slag quantity | 180,000 t/a |
Three shareholders for safe and efficient operation
Originally completely in public hands, GMVA has been operated as a public-private partnership since 2001. The City of Oberhausen is involved via its shareholder, STOAG Stadtwerke Oberhausen GmbH, and the City of Duisburg via Wirtschaftsbetriebe Duisburg – AöR (WBD). The third member of the group is the privately owned environmental service company, REMONDIS, which contributes to the company’s success with its waste management expertise.
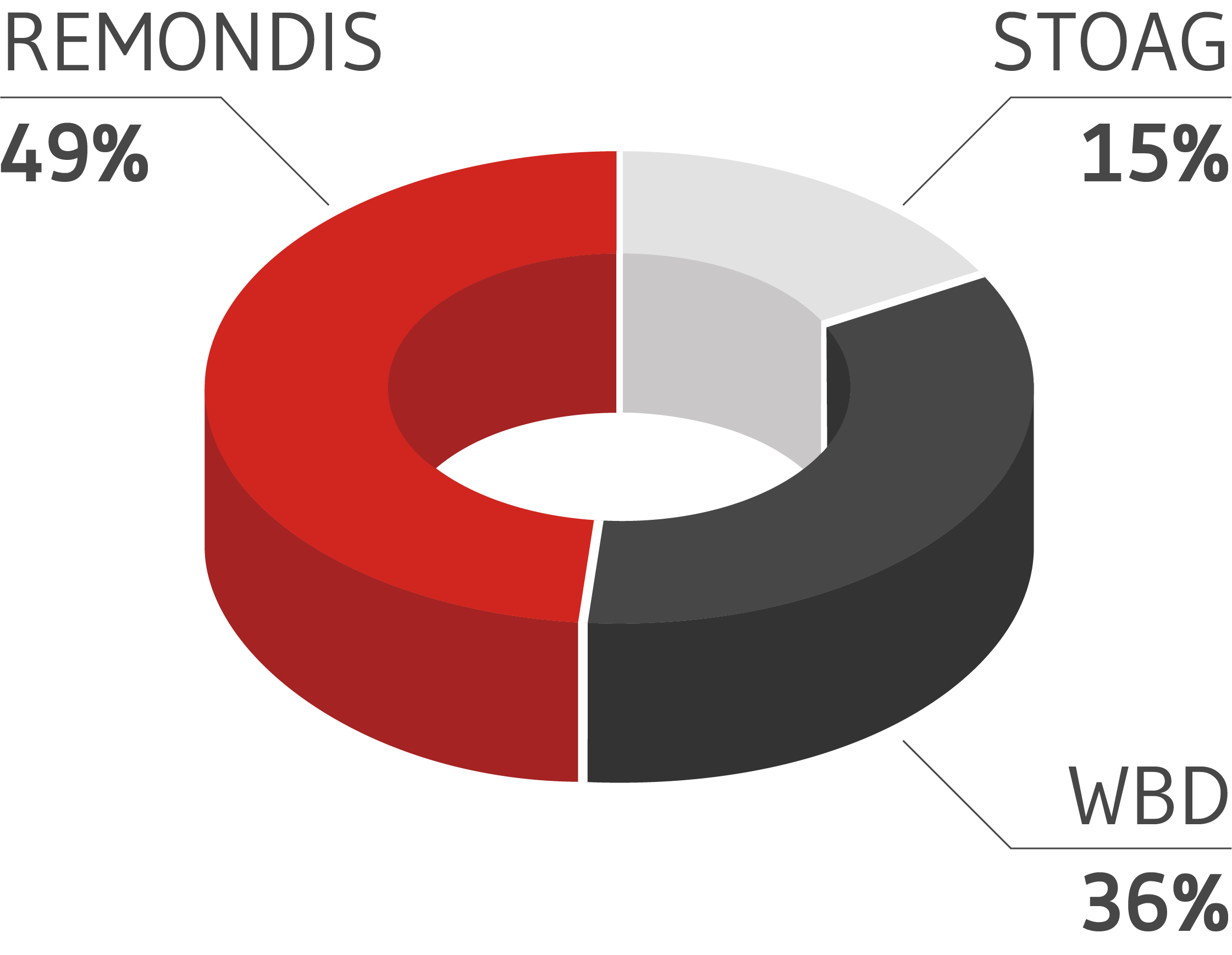
Acting responsibly, setting the direction
Acting responsibly is a central component of GMVA’s corporate culture. Profitability, sustainability, safety and mutual appreciation play a decisive role in this. This corporate culture is exemplified on a daily basis by the qualified specialists and managers on the Management Board and Supervisory Board.